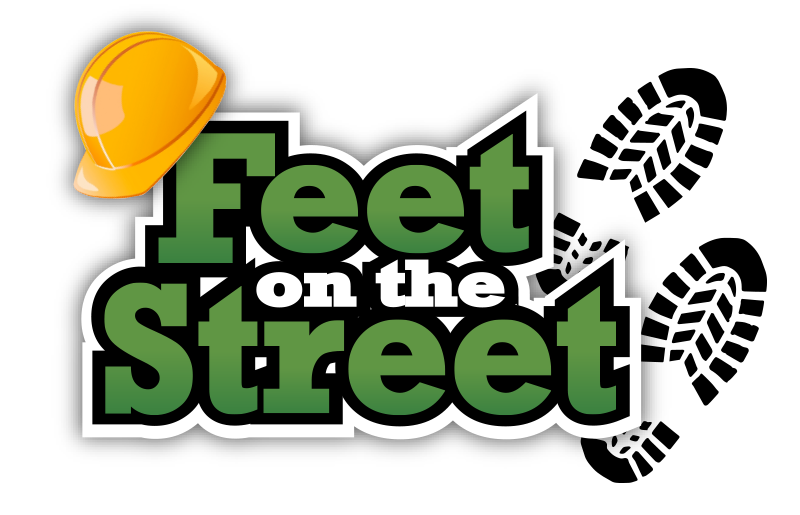
Feet On The Street – The Latest 2/24
The inverse curse: COVID-19 infections are trending downward amid sharply rising building costs. “It’s really bad.”
The Custom Home Builder’s View
“We still have COVID-19 issues — they’re not as bad as they were 30 to 60 days ago. The biggest issues are material pricing,” said a Los Angeles-based contractor and QuickDraw client when we spoke to him fresh on a Monday morning.
A builder of higher-end homes with projects located in Brentwood, Santa Monica, Manhattan Beach, Hollywood and Hidden Hills, stated: “Lumber is up, concrete is up. Lumber is really bad — it’s at historic highs. On some of our bigger houses (10,000-14,000 square feet), lumber adds an additional $70,000 to $100,000.” That $7 per-square-foot increase excludes structural steel. “Last year, we were bidding framing at $30 to $35 per square foot. Today, the number is $40 to $45. One year ago, structural steel pricing was $3.50 per pound. Today, it’s $6.”
With executed subcontract agreements in place, many subs are going back to their clients with price increases. They are unable to absorb the unforeseen sharp rise in material costs. Feet on the Street learned that in some cases, when general contractors pushed back, some subcontractors threatened to leave.
That paints a grim picture.
Framing materials aren’t the only products rising in cost — so are plumbing, HVAC, sheetmetal, drywall and finish carpentry materials. “MDF, white oak and millwork prices are going up.”
Steel pipe — a.k.a. black iron pipe — that plumbers use for gas systems is up 300%. “We’ve bought every stick of inventory in the three largest supply houses in Southern California,” said a plumbing and heating contractor with over 2,000 employees. “Copper prices are up as well.”
Year-over-year construction costs are up 10% on custom homes, with no relief in sight.
“There’s no doubt the supply chain has been impacted, but COVID-19 has also become an excuse to raise prices. My lumber salesman thinks the mills are price-gouging.”
The Production Home Builder’s Perspective
Unfortunately, the pain of rising costs isn’t limited to custom homes and is being felt across all construction platforms.
A veteran tract homebuilder told Feet on the Street: “Less than five years ago, our direct construction costs ran $57 to $58 per square foot. In Q3 2020, they were $82 and, today, they’re $84 per square foot.”
“We’re still struggling with manpower. Roofers are killing us. I’ve got driveways poured, and no roofers. That’s a two-month delay! There is no roof paper available. Home Depot only had 23 rolls in stock — that’s it.”
The supply chain trickle-down effect is having an impact. “The sheetmetal plant that supplies our subcontractor closed for 15 days. They opened up again, just to have another positive test result, and closed for another 15 days.”
Exasperated, he added, “Our plumbing supply house closed for one month. They told me it takes longer to train a replacement, so it’s cheaper to close down.”
The wild swings in manpower continue. A project sees 25 workers one day, then only three the next day. “Friday, between the framers and concrete guys, we had 150 men working on two phases. On Monday, we had only 15 cars.”
Construction schedules that were 95 days are now 150 days from trench to walk.
Conversely, the land development portion of the workforce is largely unaffected and is performing strongly. “Crews that work by themselves are okay. I’ve been watching a commercial project that I pass every day to work, and those guys are flying! In 45 days, the entire site is ready for vertical construction.”
There is still fear in the labor force. COVID-19 requirements include signing a daily log that states you have not been exposed to the virus. Very few workers are willing to sign and, if you force them to do so, they leave. Fear of any documentation in a largely Hispanic construction workforce is pervasive.
“You can’t ask anyone if they’ve had COVID. It’s against the law,” said one project manager.
It’s a very tough balancing act for project managers, superintendents and workers alike.
Cities, Counties, Municipalities and Water Districts — Entitlements, Approvals and Permits
What one client calls “the new normal” is also adding time to projects’ life cycles.
The people who work in the government agencies — the plan-checkers, and the staff who process submittal packages and issue approvals and permits — continue to work on a reduced office schedule.
In the City of Los Angeles, it used to be that if you had a ready-to-issue ((RTI) project, you could count on building permits being issued in three days. Now, it takes three weeks.
“Permits are horrible!” said one participant.
Another said, “You have to make appointments now. I walked into a city that is new to us, and they almost called the police.”
It is all no-contact. Fee payments are processed via a physical dropbox, and your check may take two weeks to process. Some agencies require you to print out your inspection cards, too.
“We’ve had to learn the local approval and permitting requirements quickly.”
Overwhelmingly, building inspections have remained consistent during COVID-19. Yes, there are protocols that must be followed but, fortunately, they are not causing project delays.
There’s some good and really good news, too.
According to our sources, many of the building materials shipped from overseas are not arriving with a new price tag and costs are holding steady. Think windows and hardwood flooring as examples.
As we all know, the real estate market is very strong. “There’s huge demand for the Los Angeles high-end homes. There’s no inventory. Two of our homes recently sold for $16 million and $9.5 million. The $2 million to $5 million market is crazy”.
Demand is not limited to the high-end market only. The entry-level and first-time, move-up markets demonstrate significantly more buyers than homes for sale. It is not uncommon to see a starter resale home garner 15 to 20 offers, or for a phase release of new homes to sell out in one weekend.
With low inventory, low interest rates, a sea-change movement to working at home, continued rise in construction costs and a 15-20% increase in construction build cycle times, the question on the table is this: How much can the market absorb?
“I read an NAHB article that said some tract home builders will pause,” said one source.
The Road Ahead
Feet on the Street asked, “Where will we be six months from now?”
“Nothing will change unless the government gets more involved with COVID-19 guidelines,” one participant stated regarding mandatory vaccinations in the workplace. “That’s the key to reduce fear and put people’s minds at ease.”
What’s Trending
Lower COVID-19 infections; inconsistent manpower; supply chain interruptions; historically high lumber and rising building costs; and a strong real estate market.
Thank you
To our trusted clients and friends, we are truly grateful for your time and help in making this important information available to our industry.