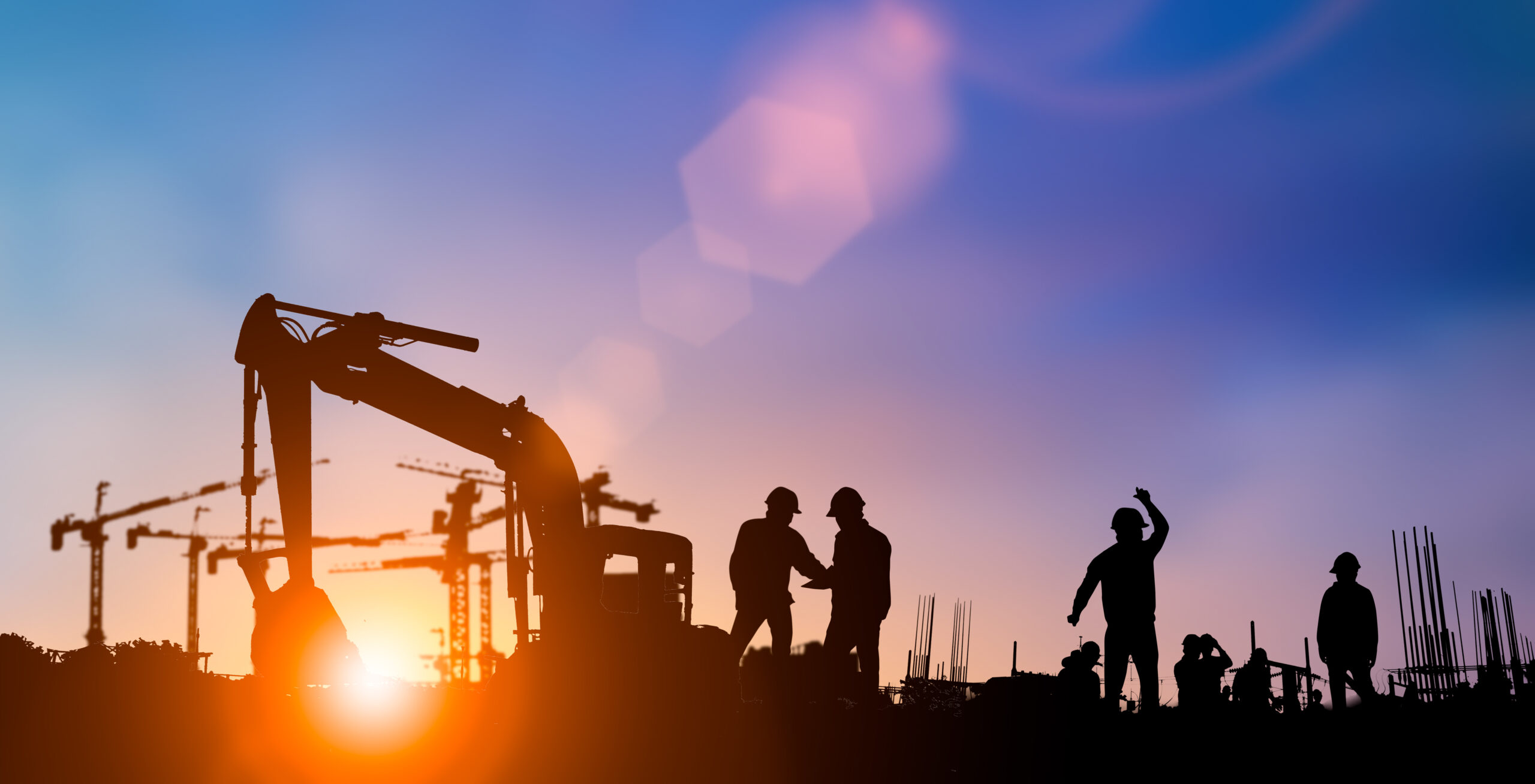
2022, The Second Half — Will Construction Costs Continue to Rise?
Looking back on 2021, many economists predicted a slow economic recovery and a potential housing crash. But not only did the housing market continue to boom, but the stock market also had a banner year, with the S&P 500 increasing by nearly 27 percent. Thanks to government assistance, many businesses were able to survive, while others actually thrived in the pandemic-spawned consumer market. Ongoing social distancing measures kept many workers and students at home, and combined with historically low interest rates, demand for housing skyrocketed.
As we enter the pandemic’s third year in 2022, the housing sector remains robust, though headwinds are starting to appear on the horizon. Due to the prevailing cycle of low inventory and high demand, both Fannie Mae and Zillow walked back their housing forecasts for 2022, predicting home price growth of 11.2% and 17.3%, respectively. And while various sources speculated that housing inventory would improve this year, inventory levels actually fell further in the early part of the year due to, in part, a wave of first-time millennial homebuyers rushing to take advantage of low mortgage interest rates. The National Home Builders Association says increasing prices could cause the cost of an average new single-family home to increase by more than $18,600 in 2022.
This year, contractors are facing many of the same obstacles as they did in 2021, with ongoing supply chain interruptions, workforce woes and soaring material costs compounded by rising inflation and interest rates.
Supply Chain
According to a recent report by the American Supply Association, supply chain congestion is improving for some sectors, but there are still nearly two million containers headed inbound into the United States. The good news is that once they arrive, inventories not affected by chronic raw material shortages will be replenished.
Sheldon Yellen, CEO of disaster response company Belfor, believes that “supply chain issues and the COVID work stoppages in some of the manufacturing facilities and plants that are producing materials are probably more significant than the actual demand itself.”
World affairs continue to cause concern as China demonstrates a new belligerence in the South Pacific, North Korea prepares for ballistic missile tests and Russia occupies Ukraine. Any of these events could further destabilize financial markets and disrupt the supply chain.
Associated Builders and Contractors Chief Economist Anirban Basu opined that since many countries do not have access to the number of vaccines that the U.S. has, there will continue to be a lag in production of materials due to COVID-19. He commented, “Even if COVID went away tomorrow and the Russia-Ukraine war ended, these supply chain troubles last into 2023 and in some cases 2024. It takes a long time to build capacity.”
Material Prices
Closely linked with the supply chain backlog is the rising cost of materials. According to the Bureau of Labor Statistics, construction material prices were up by 25% in 2021, and so far, the cost of construction in 2022 remains high. Richard Branch, chief economist for Dodge Construction Network, said he expects price increases to continue until about mid-2022 before tapering off in the latter half of the year, while other experts predict more up and down volatility throughout 2022.
Henry D’Esposito, JLL construction research lead, told Commercial Property Executive: “While everyone knows prices have been volatile over the past year, it was remarkable to visualize how severe the price swings have been this year compared to any point over the past 70 years. Not only has it been a record-breaking year for just one commodity, but commodity prices are increasing across the board.”
The increases in the prices of lumber and steel, for example, are the largest seen since the government began recording the data in 1949. The percentage of increase in the cost of plastic is the greatest since 1976.
You may relate to Yellen’s experience. He said, “Pricing, if you go back a couple years ago, OSB board was $8-9 a sheet. Over the last few months, it has gone as high as $50 to $55 a sheet.”
Oil prices are at record highs, significantly increasing transportation costs to deliver materials to the marketplace
Mother Nature has also played her part, dealing out unprecedented hurricanes, tornadoes and wildfires that have increased demand for building materials while, in some cases, simultaneously wiping out the natural resources necessary to rebuild. It has been, as they say, a perfect storm.
Copper
In the first quarter of 2021, copper prices hit a 10-year high in the U.S. Besides being used in construction materials from electrical wires to water pipes, copper is an important building component for electric cars. As governments at home and abroad push toward green energy and electric transportation technology, the demand for copper is expected to increase exponentially. To illustrate, a conventional automobile uses between 18 and 49 pounds of copper, while a plug-in electric car uses 183 pounds of copper.
Lumber
In 2021, the National Association of Home Builders reported that the price for lumber alone increased the cost of building a new home by an average of $36,000.
After the U.S. doubled tariffs on Canadian lumber and wildfires disrupted lumber production, the price of softwood lumber jumped 85% in just three months. As of January 2022, lumber was priced at more than $1,000 per thousand board feet. The Commerce Department recently made a determination to lower softwood lumber import tariffs from Canada from 17.9 percent to 11.64 percent as of August 2022. According to the Associated General Contractors of America (AGC), Canadian imports make up 30 percent of total U.S. consumption of softwood lumber.
Steel
Currently, U.S. steel prices are 70% higher than the global market price. Even accounting for the 2018 steel tariff imposed by the U.S., it would be cheaper to import steel than to buy it from domestic mills, but limited global supplies combined with shipping challenges are limiting U.S. imports and keeping prices high.
Labor
Skilled construction labor has been difficult to find since long before the pandemic, and contractors are paying a premium for it. The lack of skilled labor also causes construction delays, further adding to project costs.
According to Business Insider, the construction industry needs a “staggering 2.2 million more workers,” in the next three years, or 61,000 new workers per month, to keep up with industry demands. And it goes that competition for workers will also lead to price increases.
The United States Bureau of Labor Statistics reported that in July 2021, 4.5% of construction jobs were unfilled, totaling about 347,000 jobs. By November 2021, those figures had decreased marginally to 4.4% and about 345,000 unfilled jobs. According to Contractor Magazine, some of this shortage is attributable to the fact that more than five million people over the age of 55 exited the labor force during the pandemic, and approximately 1.5 million of those chose to take early retirement.
To remedy the shortage, industry associations are now scrambling to recruit and educate millennials and women for the construction trades. Interestingly, a report by McKinsey & Co. found that construction companies with more women in executive roles than staff roles experienced above-average financial performance when compared with companies that didn’t.
Inflation
According to Trading Economics, the annual inflation rate in the US slowed to 8.3% in April from a 41-year high of 8.5% in March, but less than market forecasts of 8.1%. Energy prices increased 30.3%, below 32% in March namely gasoline (43.6% vs 48%) while fuel oil increased more (80.5% vs 70.1%).
Fannie Mae expects Fed interest rate hikes of 25 basis points in the third and fourth quarters of 2022 and continuing quarterly through 2023. If inflation fails to decelerate in coming months, we could see more aggressive action.
Basu believes the lack of available supplies will continue to drive inflation to an even greater degree than current government projections. While the Fed is forecasting 4.3 percent inflation in 2022, Basu gauged his outlook closer to 5 percent. He said, “Along with rising wages amidst the Great Resignation, this unbalanced economy translates into higher-than-average inflation in 2022.”
Rising Interest Rates
In June 2022, the Federal Reserve approved a 0.50 percentage point rate hike, the second increase since December 2018. Rate increases are expected at each of the remaining meetings in 2022. Already, mortgage interest rates are skyrocketing. In April 2022, new data from Freddie Mac revealed that the average rate on a 30-year mortgage was 4.67% — the highest since 2018.
The National Association of Home Builders reported that high interest rates were a problem for only 2% of builders in 2021, but 31% of builders expect it to be a significant problem in 2022.
Because higher rates mean higher mortgage payments on top of inflated home prices, experts expect the housing market to cool as the year progresses. However, the prospect of more expensive loans may push consumers to purchase sooner, rather than later.
According to Fannie Mae, “The effect of buyers being priced out should mean fewer bidding wars and slower house price appreciation.”
This slowdown should provide some relief to the building sector, giving market supply a chance to catch up, at least somewhat, with demand.
Construction Loans
All of these factors combined have shifted the focus for construction lending, as builders scramble to contain costs and lenders jockey to minimize exposure to risk. Homebuilders and homeowners who commit to contracts months in advance are faced with unpredictable changes in pricing along the way. Builders are finding that new projects require higher construction costs and extended build-cycle schedules.
Expert Advice
The experts are offering some advice to help builders succeed despite current challenges. For the most part, it all comes down to good planning and sufficient capital.
Yellen advises, “Don’t say, ‘I will get it as I need it.’ You are going to have to put your money out first. You are going to have to stock and inventory a little bit, to make sure you can secure the products you need, so that each time you get to another phase of construction, you are not forced to stop working.”
Shelley Armato, CEO of MySmartPlans and manager of more than $12 billion in construction projects, said, “I would advise them to be able to track, track, track. Organize, archive, screenshot, and keep everything in one central location. Make sure that they are preparing to defend the project because the project is one thing, but it’s the lifecycle.”
A Positive Outlook on the Future
While there are likely to be more challenges ahead, the construction industry’s future is not all gloom and doom. Steve Stouthamer, an executive vice president with Skanska USA Building, said, “History shows that steep periods of construction inflation are followed by similar periods of recessed construction costs, which is attributed to the reality that higher pricing can slow or stall projects, reduce demand and increase supply.”
And there are some positive indicators on the horizon. For one, there will be plenty of work for the construction industry. The $1.9 trillion American Rescue Plan Act, passed in March 2021, contains $10 billion for critical capital projects to provide communities with access to high-quality modern infrastructure. Many of these projects are slated to begin in 2022. In addition, the Infrastructure Investment and Jobs Act, passed in November 2021, directs $550 billion in new federal funding to transportation, water, and power infrastructure.
There is also good news ahead regarding the cost of steel. President Biden has agreed to allow the UK to import more than 3 million annual tons of steel tariff-free. Similar concessions are being discussed for Japan and Korea.
Believe it or not, there is a positive side of inflation, since higher prices of consumer goods are likely to force people back to work, potentially relieving some of the labor shortages.
Basu also waxes optimistic about the commercial construction sector. “After declining during much of the pandemic, spending in the office segment has stabilized and is up 3.3% from a year ago,” he said.
“The best-case scenario for construction would be continued demand for new projects combined with stabilization in material costs. If global supply chains can return to a healthier balance by early 2022, it would bring considerable relief to pricing uncertainty and lead times for construction,” D’Esposito said.
With active projects across the U.S., Greg Norris, president of Quick Draw said “On a weekly basis, we communicate with our clients and industry contacts to monitor changes in the marketplace. This vital, real-time information is shared with to our lenders, borrowers, and general contractor clients to assist them in achieving the shared goal of a successful project”.
QuickDraw is the trusted fund control partner for residential, commercial, and industrial construction projects of every size, style and price point. From coast to coast, QuickDraw works to make the fund disbursement process a positive experience for all, with an array of related services, including: Fund Control, Site Inspections, Cost Reviews and Portfolio Management.